President*s Design Awards 2016, Designer of the Year: Rene Tan
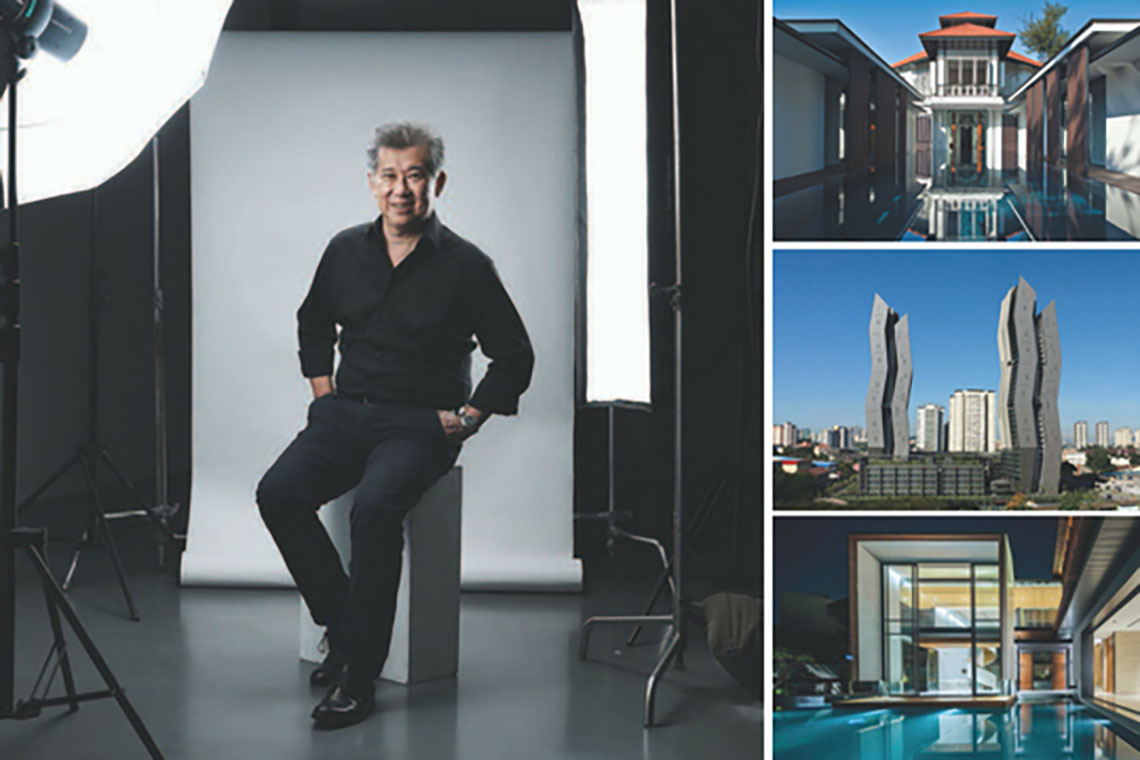
Rene Tan is the quintessential Renaissance man. He is an architect steeped in the intricacies of his craft, and yet equally fluent in other disciplines. Born in Malaysia, he earned his Bachelor of Arts in Music and Architecture from Yale, and his Master of Architecture from Princeton. His training in music has been an immense influence in the way he approaches architecture at RT+Q, the firm he co-founded in 2003. Each project is an attempt to find a rhythm of space and melody of proportion that seeks to bring order to chaos- a favourite theme in his work.
On the philosophy that guides him
“We have core values that guide our work – specifically, proportion, scale and hierarchy. These are based on the Vitruvian principles of firmitas, utilitas and venustas which, loosely translated, means every design must be solid, useful and beautiful.”
On the evolution of his approach to design
“I realised it is important to identify the concept before executing the details. This insight came to me as I studied Chopin’s 24 Etudes for Piano. Each piece literally studies a different aspect of music, be it arpeggios, octaves, thirds and so on. Each intimate piece has a point to make. When combined, they create the whole piece. This is why, today, right at the very start of any project, we don’t do anything till we have identified the challenges that need to be overcome.”
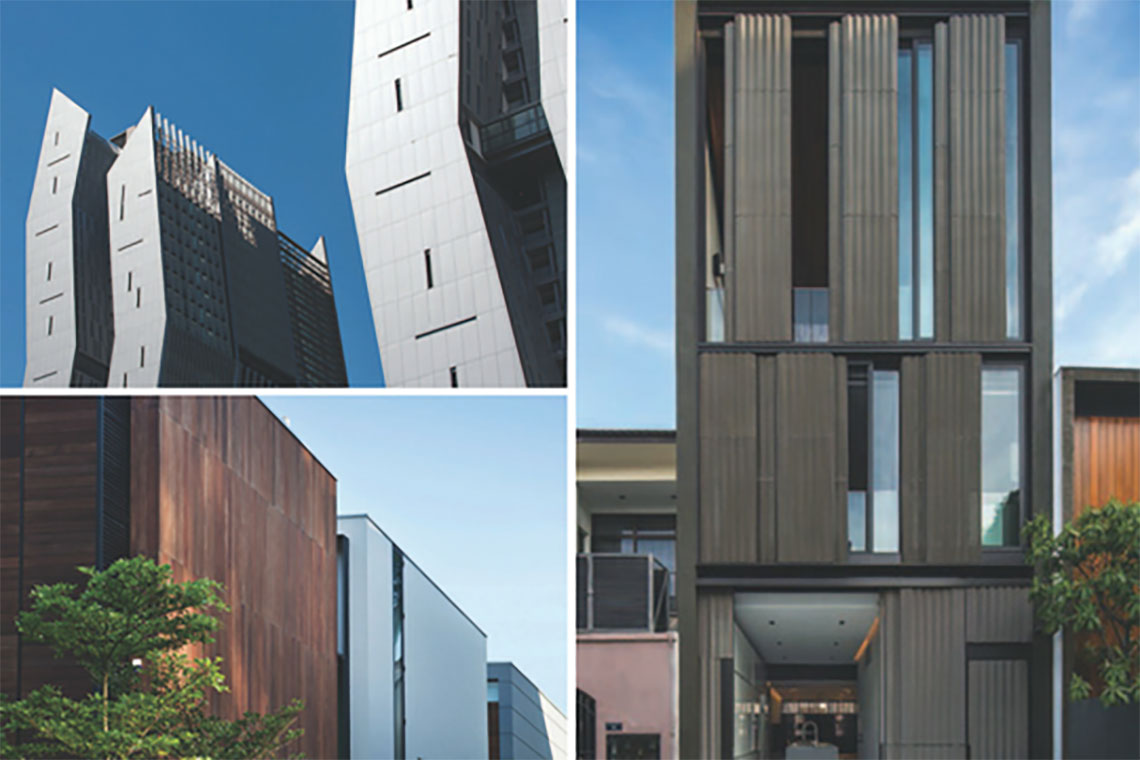
On space that make him happy
“I am most happy when I find myself in quiet spaces like a library or a gallery- where my mind is at ease and where my thoughts can roam. The dual phenomenon of space and silence is powerful.”
On which particular space best expresses his idea of the perfect urban space.
“At the top of my list is Louis Kahn’s great courtyard of the Salk Institute in La Jolla, California.”
On the social gap he would like to address through design and how.
“I’ve always wondered what architecture is like for people who cannot see. I think it would be interesting to design a facility for the visually handicapped. That would really test a few fundamental presumptions we have of architecture, particularly because it is a visual discipline.
So, what if we were to take away the visual aspect in our design and focus instead on the other senses of touch, smell, hearing and so on, so that we create an environment that is even more dramatic and sensorial? This raises interesting questions about what architecture has been, and what it could be.”